Effects of non-uniform temperature distribution on critical member temperature of steel tubular truss
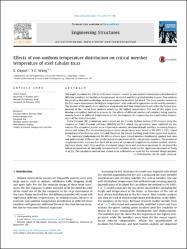
Göster/ Aç
Erişim
info:eu-repo/semantics/openAccessTarih
2016Erişim
info:eu-repo/semantics/openAccessÜst veri
Tüm öğe kaydını gösterÖzet
This paper examines the effects of thermal restraint, caused by non-uniform temperature distribution in different members, on the failure temperatures of critical members of steel tubular trusses. Non-uniform temperature distribution develops in trusses exposed to localised fire attack. The truss member nearest to the fire source experiences the highest temperature, with reduced temperatures in the nearby members. The number of the nearby truss members being heated and their temperatures will affect the failure temperature of the critical truss member which has the highest temperature. The aim of this paper is to develop a simplified method to account for the effects of different numbers of members being simultaneously heated to different temperatures on the development of compression force and failure temperature of the critical member. Finite Element (FE) simulations were carried out for Circular Hollow Section (CHS) trusses using the commercial Finite Element software ABAQUS v6.10-1 which has previously been validated by the authors. The simulation trusses were subjected to constant mechanical loads and then increasing temperatures until failure. The elevated temperature stress-strain curves were based on EN-1993-1-2 [1]. Initial geometrical imperfections were included, based on the lowest buckling mode from eigenvalue analysis. The numerical study examined the effects of truss type, critical member slenderness, applied load ratio and axial restraint stiffness ratio on the failure temperatures of the critical truss members. The numerical simulation results were used to check the accuracy of a proposed simplified calculation method, combining linear elastic static truss analysis at ambient temperature and analytical equations to calculated the failure temperatures of thermally restrained truss members based on the regression equations of Wang et al. [2]. The calculation method was shown to be sufficiently accurate for fire resistant design purpose. (C) 2016 Elsevier Ltd. All rights reserved.