The effect of high B4C ratio on the improvement of mechanical properties and wear resistance of Al2024/B4C composites fabricated by mechanical milling-assisted hot pressing
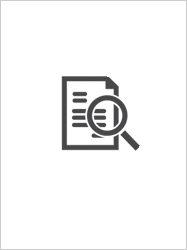
Erişim
info:eu-repo/semantics/openAccessTarih
March 2025Erişim
info:eu-repo/semantics/openAccessÜst veri
Tüm öğe kaydını gösterKünye
Scopus EXPORT DATE: 17 March 2025 @ARTICLE{Beder20259528, url = {https://www.scopus.com/inward/record.uri?eid=2-s2.0-85215542884&doi=10.1016%2fj.ceramint.2025.01.287&partnerID=40&md5=5d7eac7a67b56d3af693510b0682e480}, affiliations = {Gümüşhane University, Department of Mechanical Engineering, Gümüşhane, Turkey}, correspondence_address = {M. Beder; Gümüşhane University, Department of Mechanical Engineering, Gümüşhane, Turkey; email: muratbeder@gumushane.edu.tr}, publisher = {Elsevier Ltd}, issn = {02728842}, coden = {CINND}, language = {English}, abbrev_source_title = {Ceram Int} }Özet
In this study, the effects of 0 wt% (C0), 10 wt% (C1), 20 wt% (C2) and 40 wt% (C3) B4C content on the microstructure, mechanical properties and dry wear properties of Al2024/B4C composites were investigated. In order to prepare Al2024 matrix composites with different B4C particle contents, mechanical milling (MM) and hot pressing (HP) were employed as powder metallurgy methods. It was found that the θ (CuAl2) phase content in the microstructure of Al2024/B4C compact materials increased with increasing B4C particle reinforcement, reaching its highest value at 40 wt% B4C (C3) reinforcement ratio. As the B4C particle reinforcement content increased, the hardness values of the composite samples increased. Flexural strength values were 445.30 MPa, 495.20 MPa, 277.59 MPa, and 129.37 MPa for samples coded C0, C1, C2, and C3, respectively. It was found that the C0 sample without particle reinforcement exhibited more than 10 times the volume loss of the C3 sample with the highest particle reinforcement at 450 m sliding distance. The SEM examination of the friction surfaces of the Al2024/B4C composite samples showed that the worn surfaces were composed of delamination, adhesion and smearing layers. © 2025
Bağlantı
scopus.com/record/display.uri?eid=2-s2.0-85215542884&origin=SingleRecordEmailAlert&dgcid=raven_sc_affil_en_us_email&txGid=c00dd9591c40081966d3d6e727f99c32https://hdl.handle.net/20.500.12440/6479